空压系统能效测试实施流程及案例分析
+ 查看更多
作者简介:
郑杰,机械设计制造及其自动化专业,万泰认证能源事业部项目经理,拥有5年工业企业节能技改、能源管理经验,3年能源咨询项目经验,熟悉GB23331能源管理体系辅导、能源审计流程及技术要求。曾负责延长石油、彩虹(延安)新能源股份有限公司企业能源审计、公共机构能源审计项目,参与多个绿色数据中心认证、PUE测试、工业节能诊断工作。擅长供配电系统、锅炉系统、压空系统、照明系统、供水系统、流体循环系统的现场勘测、能效诊断测试、节能潜力寻找。
空压机耗电量大,占工厂用能的15%左右。空压机系统改进潜力大,通过测试空压机的能效,可以判断空压机系统的运行效率,查找压缩空气干燥、输送等环节的损耗,挖掘出节能改善潜力。
空压机能效测试前,工作人员应熟悉所测试空压设备管道区域受否满足测试要求,并在管道上焊接螺纹头,准备好测试工作所需相关材料、仪器仪表、工器具、相关图纸、试验报告、及相关技术资料。
同时确保测试要求仪器仪表、工器具应试验合格,满足施工的要求,各类辅助材料应齐全,图纸及资料应附合现场实际情况。
1、测试项目和操作标准流程
+ 查看更多
1、测试点位的选择:必须在竖直或水平的管道上,距离弯头较远,且管道距离地面较近,并确保至少有一侧存在2米的空间,易打孔及流量计安装。
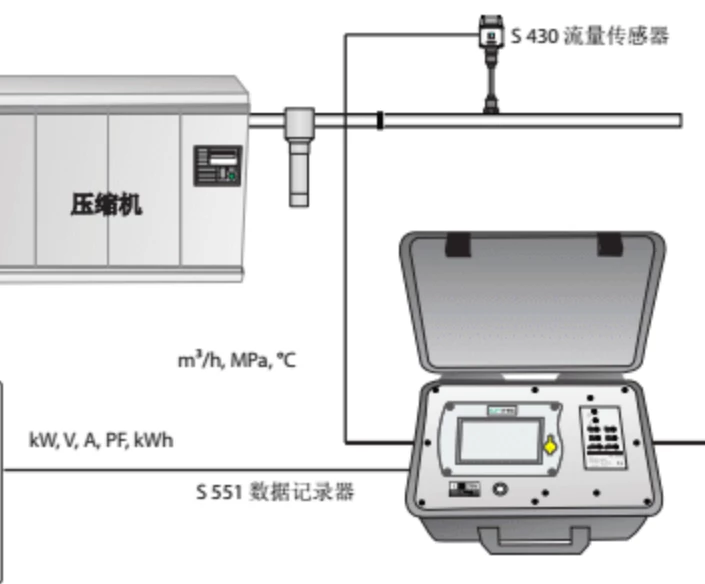
2、在管道上焊接螺纹头,螺纹头规格:G3/4,公制螺纹。
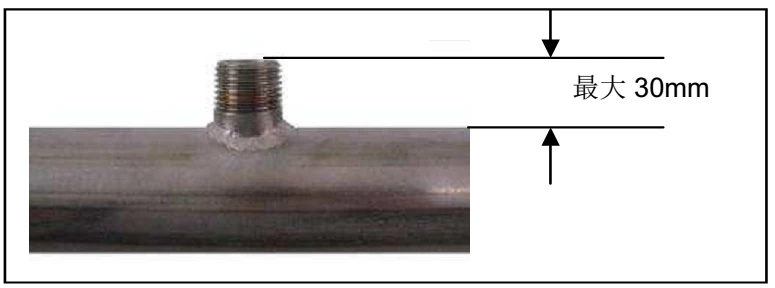
3、将球阀安装到螺纹头上,关闭球阀
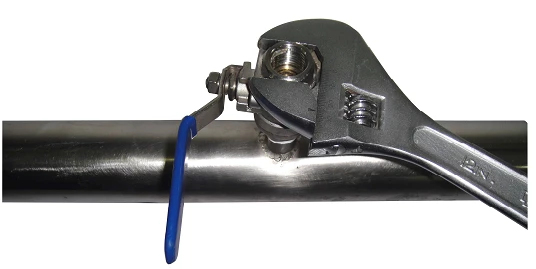
4、将带压打孔器链接电钻固定到球阀上,进行带压开孔,开孔过程中需注意钻头冷却,需每钻15S,后退10S,以防磨损。
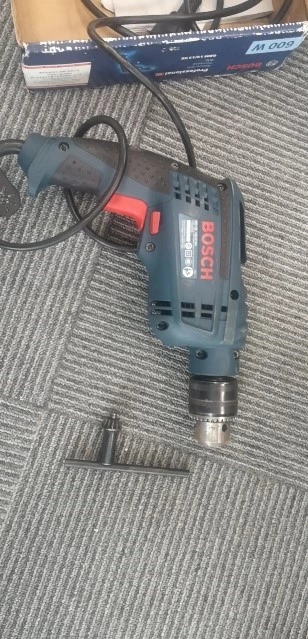
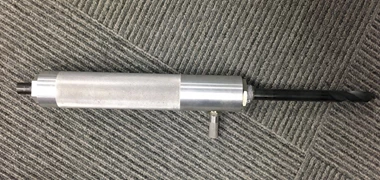
5、完成开孔后将流量计安装到球阀上。
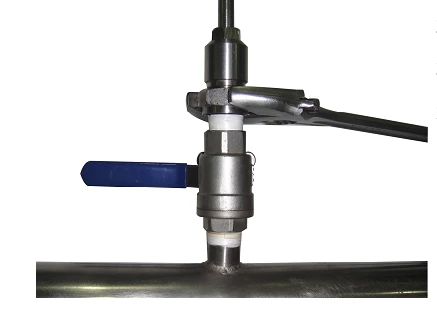
6、打开球阀,检查是否有气体泄漏,如果没有泄漏则将球阀完全打开。
7、将流量传感器插入管道中心,插入深度按下图所示计算。
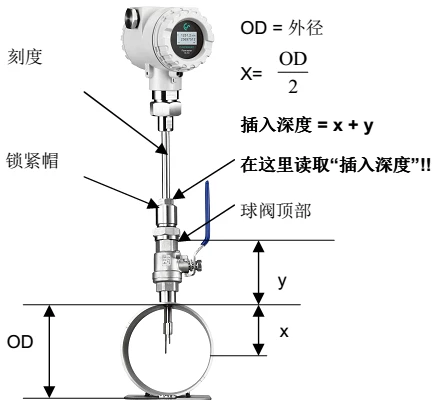
8、完成安装后进行检查,确认设备安装正常后进行接线。
9、测试完成后,拆下流量计,关闭球阀。
9、测试完成后,拆下流量计,关闭球阀。
2、测试案例分析
+ 查看更多
1)空压机制气过程能源转换效率测试
某炼油企业两台空气压缩机额定功率2265KW,测试期间开启2台空压机正常且满负荷运行,实际总功率1966kW,因两台设备出气口弯道较多,无2米以上的水平竖直的管道,故在流量总管上进行了打孔安装测试,测定两台空压机总流量19565.2m3/h,计算得到比功率6.03kW/(m3/min)。具体参见表1和表2。
某炼油企业两台空气压缩机额定功率2265KW,测试期间开启2台空压机正常且满负荷运行,实际总功率1966kW,因两台设备出气口弯道较多,无2米以上的水平竖直的管道,故在流量总管上进行了打孔安装测试,测定两台空压机总流量19565.2m3/h,计算得到比功率6.03kW/(m3/min)。具体参见表1和表2。
表1测试压缩机配置情况表
序号 | 设备名称 | 设备型号 | 流量 (m3) | 额定 功率 | 生产厂家 | 投用日期 | 备注 |
1 | 离心式压缩机 | ZH1250 | 11388 | 1250 | 阿特拉斯 | 2018.01 | 二空 |
2 | 螺杆空压机 | ZR900VSD-8.6 | 7500 | 1015 | 阿特拉斯 | 2016 | 空压站 |
表2 空压机运行效率
机台 | 4# | 6# |
排气量(m³/h) | 19565.2 | |
实际功率(kW) | 1966 | |
比功率(kW/(m³/min)) | 6.03 | |
电气比(kW/m³) | 0.100 |
从空压机比功率及电气比测试结果看,该企业空压机系统制气过程能源转换效率处于正常水平。
2)压缩空气干燥损失测试
某炼油企业干燥系统采用微热再生吸附式干燥机,使用后的压缩空气直接排空,经测试:压缩空气干燥前流量19565.2m3/h,干燥后14454.8m3/h,损失达5109.8m3/h,损耗量达26.12%。具体参见表3。
若该企业采用余热再生的零气耗干燥系统,根据现场测试数据,在仅开2台空压机的情况下,压缩空气干燥前后损失量达5109.8m3/h,按气电比0.1kW/m3计算,年可节约用电量=5109.8*24*365*0.1/10000=447.62万kW·h。
表3 压缩空气干燥损失计算
机台 | 4# | 6# |
干燥前排气量(m³/h) | 19565.2 | |
干燥后排气量(m³/h) | 14454.8 | |
损失量(m³/h) | 5109.8 | |
损失率 | 26.12% |
3)使用过程损失测试
某新能源企业玻璃炉窑采用富氧燃烧,共有4台离心压缩机用于制压缩空气并分离压缩空气制氧,4台设备均满负荷运行,无任何变频措施,在生产未满负荷的情况下,因不确定氧气流量需求下降多少,仍采用满负荷运行,多余氧气选择直接排空。经现场测试,氧气供气流量为11736m3/h,终端实际使用量仅8890m3/h,氧气排空量达2846m3/h,排空率达到24.25%。具体参见表4。
表4 压缩机配置情况表
序号 | 设备名称 | 额定流量(m3/h) | 额定功率 | 状体 | 供气压力MPa |
1 | 离心式压缩机 | 16500 | 1500 | 在役 | 0.57 |
2 | 离心式压缩机 | 16500 | 1500 | 在役 | 0.57 |
3 | 离心式压缩机 | 16500 | 1500 | 在役 | 0.57 |
4 | 离心式压缩机 | 16500 | 1500 | 在役 | 0.57 |
通过流量测试发现,该企业正常可减少一台压缩机的运行,可减少约1500KW的功率消耗,按照每天24H计算,则每天可节约用电=1500*24=3.6万kW·h,按0.56元/kW·h计算,可日节约用电费用约2万元,年可节约用电成本600万元。
通过上述案例分析可知,对空压系统进行能效测试,能够及时发现空压系统在制气、干燥、输送等环节存在的问题,如果及时采取管理或技改措施,能够有效的实现企业空压系统节能降耗及降本增效。